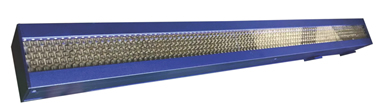
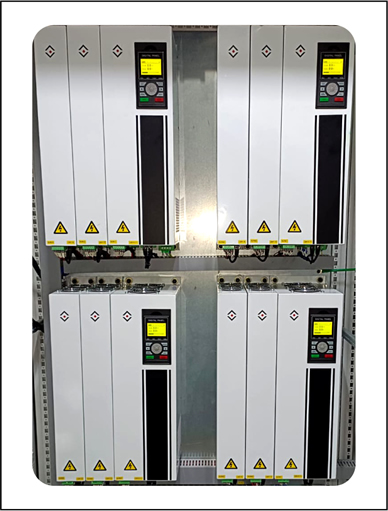
LED UV curing application principle
With the polymer makeup of LED inks & varnishes & the low heat of the UV diodes, higher gloss levels can be achieved. Higher colorfidelity and sharpness is achieved through trapping and flash curing the ink on the surface of the stock. When an LED ink cures, it forms a polymer chain that protects the sheet, it is no longer water soluble, and it resists most solvents. Coatings and vamishes (OPV) can be used to flood or spot coat the sheets.
The full benefits of LED printing, such as variable intensity dosing segmented output, and programmable data communication with the machine are made possible with the SPECTRUM UV Light+Control (LC) LED Control System. Capable of driving lamps from the smallest sheet sizes to large formats, the LC Control Systems is designed for full programmable control of the LED lamps, maximum protection of the LED system, and a compact footprint for easy placement.
When printing with LED UV and polymer inks, no spray powder or heat is required to accelerate drying time on the press. Expensive and problematic cylinder jackets are not required when printing in perfecting mode, and drying problems are eradicated on nearly all stock types, including gloss and matte coated papers, uncoated offset papers, paperboard for packaging, non-porous synthetic papers, foil-laminated sheets, and plastics such as lenticular as well as most plastic packaging, card and label stocks.